Cool Tech
Data centers are the invisible heroes of our modern digital age. Their presence enables our communications, streaming, downloading, research, work, and play 24 hours a day, 365 days a year. As of 2020, there are around 20 Billion devices currently connected to the internet. These centers serve as crucial hubs for data transmission and storage, and they are becoming larger and more advanced every year.
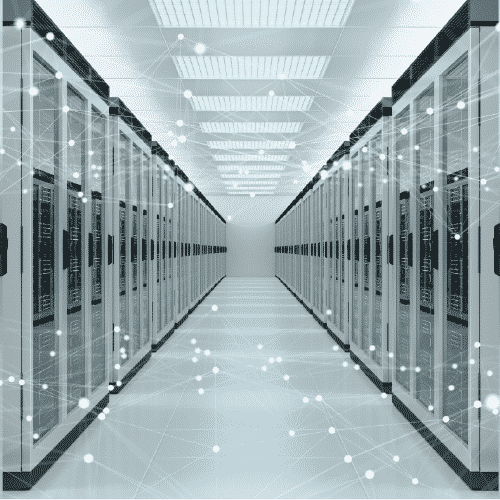
For all electronic and mechanical equipment, greater power consumption equals greater thermal output. Therefore the larger the data center, the more waste heat needs to be removed. Overheating servers crash, go off-line, corrupt data, and can damage expensive hardware. Let’s take a look at the specialized world of data center thermal management.
Ideal Server Environment
Ideally, server rooms and data centers should be kept around 72° F with 45% relative humidity. Computer servers can tolerate slightly higher temperatures (up to 90°), but that leaves no room for heat spikes that can occur due to equipment malfunction, or even an exterior door being left open.
Chilled Inside and Out
Data center cooling begins deep in the heart of the hardware itself. As internal CPU components generate heat, that heat is collected into a heat sink. From there, fans or liquid cooling tubes transfer the heat outside the computer’s case. Once the server’s waste heat is dispelled into the ambient air, it needs to be removed from the data center itself. From here, industrial air chilling units cool the ambient air and expel the waste heat from the building.
Innovative Heat Dispersal
Some tech companies have innovated environmentally safe ways to reuse this heat instead of just dispersing it into the atmosphere. Repurposing heat also helps fight the perception that data centers are heartless energy hogs. Here are just a few examples of how data centers recycle waste heat:
- Facebook’s data center in Odense, Denmark pipes waste heat to over 7,000 local homes
- Telecity’s data center in Paris, France heats an onsite arboretum
- The University of Notre Dame reuses the heat from from their Research Computing Center to heat a greenhouse and botanical garden
Cool Design Features
Data centers are specially engineered for the strategic flow of cool and hot air. By carefully managing layout and exhaust port orientation, data centers can optimize every BTU of cooling power.
Raised Racks/Floors
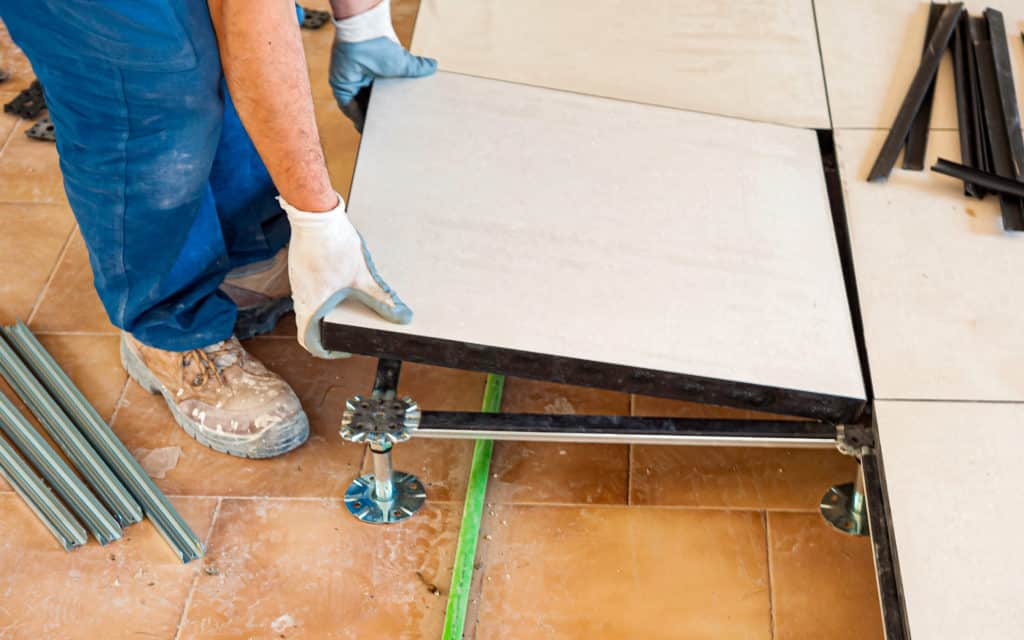
Data centers often house their server racks on double layered raised floors to facilitate cooling. Cables and wiring are run through the negative space between a concrete subfloor and a removable panelled top floor. Not only does this make it easier for technicians to access wires and cables for inspections and repairs, but this also improves airflow throughout the server room.
Cool air is forced between the floors and can exit through strategically placed perforated tiles. Perforated tiles are placed next to server rack front and allow cool air flow up into the server room. Efficient air flow is critical for data center cooling management.
Hot and Cold Aisles
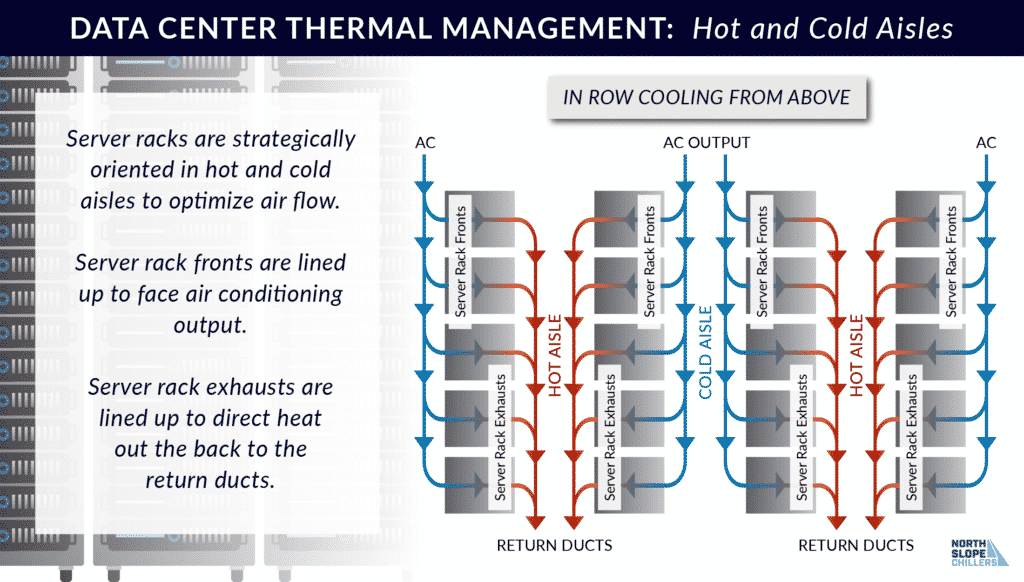
To save energy and optimize air flow, data centers organize their server racks to create hot and cold aisles. Server rack fronts are lined up to directly face air conditioning output. Cold air flows through the server racks removing heat and expelling it out the exhaust in the back. Server rack exhausts are lined up to directly face the ac return ducts.
Immersion Cooling
Some data centers have begun experimenting with immersion cooling. This cooling method involves completely submerging server racks into tanks filled with dielectric liquid or oil. Dielectric fluids are specialized non-conductive liquids through which no electric current can pass. They can electronically insulate even high voltage equipment and prevent arcing. When this fluid is chilled, it also acts as a liquid coolant for the running servers.
North Slope Chillers Data Center Cooling Solutions
Redesigning server room layouts is expensive and creates problematic downtime. North Slope Chillers is proud to offer powerful portable server room chilling that is easy to install without altering your current system. With a wide range of cooling capacities, we can provide you with the exact temperatures you need to continuously keep your servers running cool. Contact us to find the right server room cooling solution for your needs at (866) 826-2993 or [email protected]