We think vaccines are pretty cool. Unlike most medicines, which treat or cure diseases, vaccines actually prevent them. Thanks to vaccines, many life-threatening diseases have now been nearly eradicated. However, with great power comes great responsibility; effective vaccines require careful temperature control from creation to administration to remain effective.
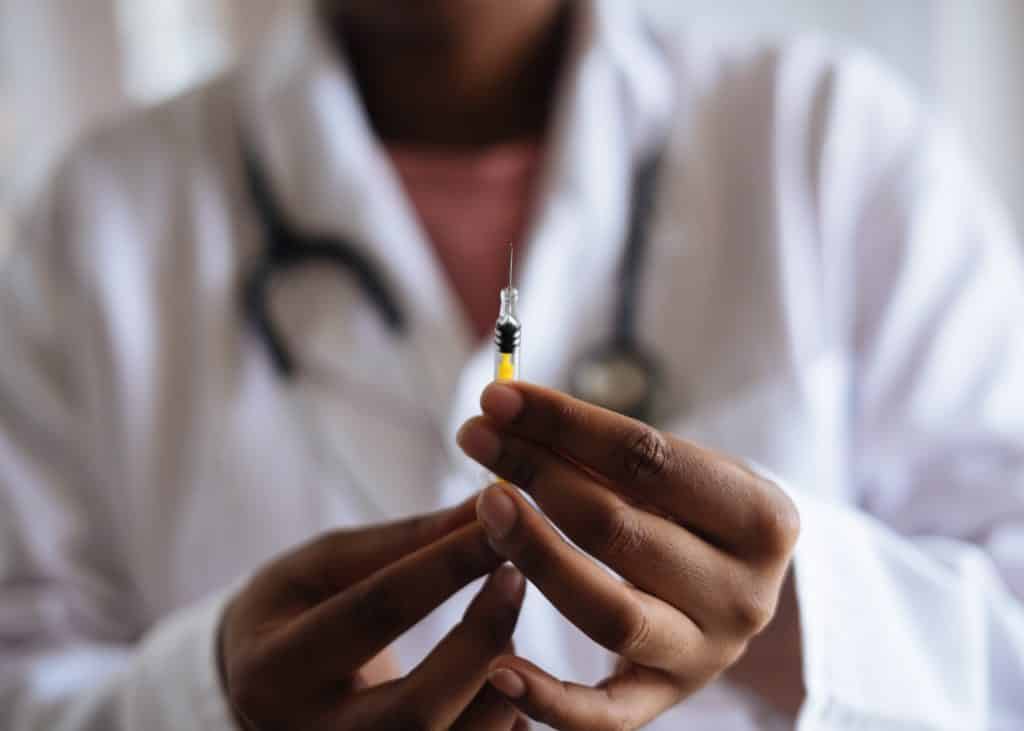
How Do Vaccines Work?
Vaccines contain the same germs that cause disease. (For example, measles vaccines contain the measles virus) That may sound a little scary, but the germs in vaccines have been either killed or carefully weakened enough to not make the recipient sick. Some vaccines even contain just part of the germ.
The killed or weakened virus stimulates the immune system which then produces antibodies. After getting vaccinated, recipients develop immunity to that disease without having to get the disease first.
How Vaccines are Made
A few basic methods are used to produce vaccines. Let’s take a look at them and the benefits and limitations of each.
- Weaken the virus
For this method, viruses are weakened so that they won’t be able to reproduce enough to cause illness. While viruses typically reproduce thousands of times during an infection, weakened viruses in vaccines typically reproduce fewer than 20 times. While this isn’t nearly enough to get someone sick, it is enough to induce “memory B cells” that protect against infection in the future.
The vaccines for measles, mumps, rubella, rotavirus, oral polio (not used in the U.S.), chickenpox (varicella), and influenza (intranasal version) vaccines are made this way.
This approach to creating vaccinations has the advantage of providing life-long immunity after just one or two doses. Unfortunately, vaccines with weakened viruses typically cannot be given to those with weakened immune systems (i.e. cancer or AIDS patients)
- Kill the virus
Using this strategy, viruses are chemically killed. The dead virus cannot possibly reproduce or cause disease. However, the virus is still recognized by the body and the immune system produces cells that protect against disease.
The hepatitis A, polio, influenza (shot version) , and rabies vaccines are created this way.
These vaccines have the advantage of not causing even a mild form of disease, which means they can be given to those with extremely fragile immune systems. The limitation of this method is that it typically requires several doses to achieve immunity.
- Use part of the virus
In this approach, the vaccine is made from a protein found on the surface of the virus. This strategy can be used only when an immune response to one part of the virus (or bacteria) causes protection against disease.
One shingles vaccine (Shingrix®),The hepatitis B vaccine, and the human papillomavirus (HPV) vaccine are created this way.
These vaccines can be given to people with weakened immunity and appear to facilitate life-long immunity after only two doses.
Vaccines and Temperature Control
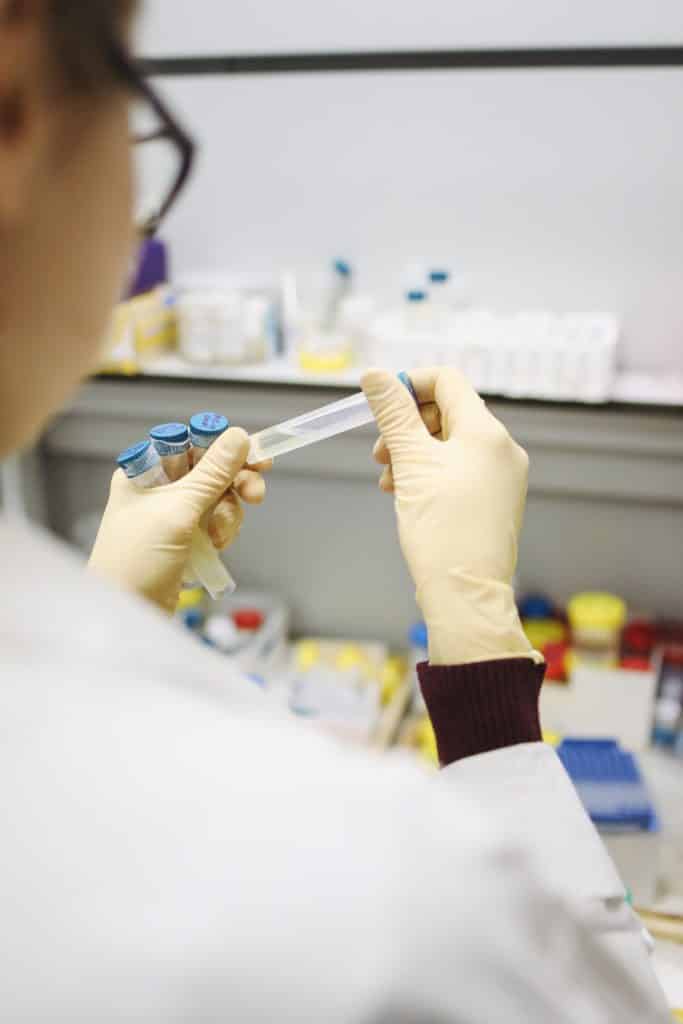
Keeping vaccines at the correct temperatures during storage and handling is an essential factor in preventing many diseases. Failure to regulate a vaccine’s temperature can reduce its potency, resulting in inadequate immune responses in patients and reduced protection against diseases.
A vaccine’s cold chain begins with the cold storage unit at the manufacturing plant and ends at vaccine administration. Every step of handling and storage in between must be carefully temperature controlled.
In the cold chain, too much exposure to heat, cold, or light at any step can damage vaccines.The more exposure, the more they are damaged. For refrigerated (not frozen) vaccines, a single exposure to freezing temperatures can completely destroy the potency.
Storage and handling temperature errors can cost thousands of dollars in wasted vaccines and revaccination. They can also cause loss of patient confidence when repeat doses are necessary.
Guidelines for temperature monitoring and storage
According to the CDC, refrigerated vaccines should be stored at 40°F. Temperatures outside the range of 36-46°F must be immediately reported. Never freeze refrigerated vaccines.
Frozen vaccines must be stored in a freezer set to the factory or mid-point settings. Temperatures outside the range of -58-5°F must be immediately reported.
The CDC provides the following additional guidelines for the storage and handling of refrigerated and frozen vaccines:
- Place the vaccines in trays or containers for proper air flow.
- Put vaccines that are first to expire in front.
- Keep vaccines in original boxes with lids closed to prevent exposure to light.
- Separate and label by vaccine type and public (VFC) or private vaccine.
- Record refrigerator or freezer temperature settings daily
- Keep the refrigerator or freezer door closed
- Use water bottles in the refrigerator to help maintain consistent temperature.
- Leave 2 to 3 inches between vaccine containers and refrigerator walls.
- Post “Do Not Unplug” signs on refrigerator or freezer and near electrical outlet.
- Don’t use dormitory-style refrigerator or freezer.
- Don’t use top shelf for vaccine storage.
- Don’t put food or beverages in refrigerator.
- Don’t put vaccines on door shelves or on floor of refrigerator.
- Don’t drink from or remove water bottles
North Slope Chillers provides cooling solutions (including custom solutions) for anything that needs to be carefully chilled. Give us a call at (866) 826-2993 if you have any questions or want to learn more!