Uncharted Territory
The COVID-19 pandemic has introduced a slew of challenges for the industrial community. With whole economic sectors shuttered, bottlenecks and deficiencies in the supply chain, drastic changes in consumer behavior, roller coaster stock market figures, collapsing oil demand, furloughed work forces, and new health and safety restrictions…companies are reeling to steady their ships.
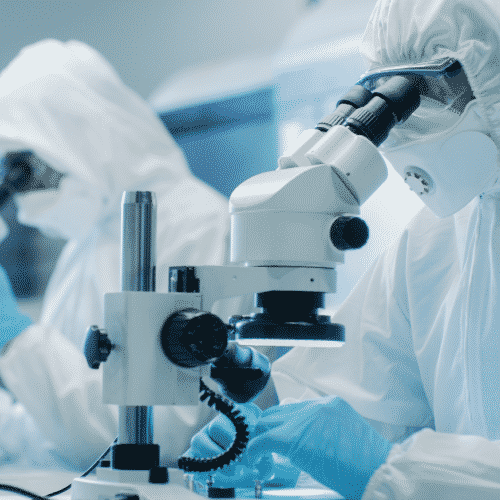
The full breadth and complexity of these challenges have already caused immense implications for even those companies who had contingency plans on file. Typical emergency plans usually cover power outages, natural disasters, and security compromises. However, the current COVID-19 situation is changing so rapidly, the manufacturing sector is struggling to protect themselves during such a widespread and extended global crisis.
Manufacturing Ramifications
The National Association of Manufacturers conducted a survey (from Feb.28th – Mar 9th) among leading manufacturers to get a feel for how the industry will be affected by the current pandemic.
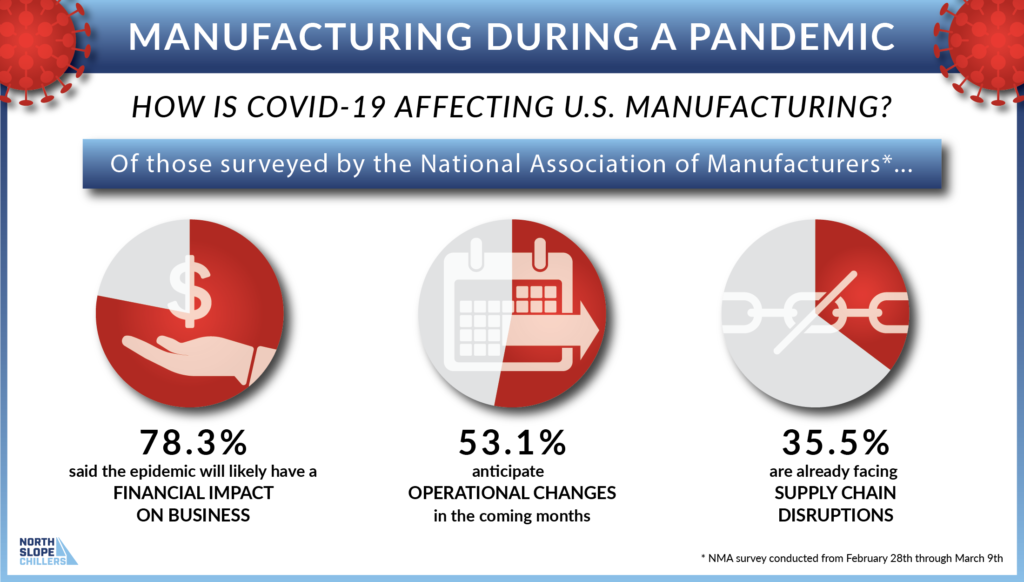
78.3% of those surveyed said the COVID-19 epidemic will likely have a financial impact on their business. 53.1% anticipate a change in their operations in the coming months. 35.5% are already facing disruptions in their supply chain.
Unprecedented Challenges
Manufacturers are trying to find ways to allow employees to work remotely, fill orders on time, maintain their product quality while making compromises, store materials longer than usual, create safe distances in worker dense spaces, and prepare for supply chain adjustments.
The food and beverage industry is one sector that has experienced the most upheaval as the supply and demand chain has developed some unfortunate kinks. While grocery store suppliers are ramping up production to meet demand, food suppliers that cater to restaurants, theme parks, hotels, cruise liners, and schools have found demand cease almost overnight. These suppliers have been left with excess inventory and lack the cold storage capacity to store it while finding new customers. The result is a staggering increase in food waste.
Necessity is the Mother of Invention
During the years following the attack on Pearl Harbor, American production and manufacturing changed completely. Clawing its way back from a period of inactivity during the great depression, the country suddenly found specific industrial demands skyrocketing. Some manufacturers simply ramped up production, while others switched gears entirely.
Car manufacturers began churning out fuselages, guns, and tanks. Sheet metal factories pivoted to solely producing parts needed for constructing ships, planes, and other defense vehicles. Consumers rationed and planted victory gardens so more domestic food supplies could be diverted to support our armed forces. The majority of the country unified their priorities, and refined their focus to the war effort.
Switching Gears
As global needs and consumer habits have completely changed in the last several weeks, some manufacturers have resurrected a good old “war time” mentality and shifted production practices. Dozens of craft distilleries have re-directed their alcohol production from spirits to hand sanitizer. Fashion designers and clothing manufacturers have set to work sewing PPE (personal protective equipment) for health care workers.
Family history geneticists have turned their saliva based ancestry kits into more affordable, FDA approved COVID-19 tests. Vacuum manufacturers have pivoted their technology to producing ventilators. Automobile factories have rededicated their production floors to creating face shields. The tech industry is even redirecting computing power to epidemiology labs to help them run molecular sequencing programs more quickly.
Selling Raw Materials
Some manufacturers have adjusted by selling raw materials directly to clients instead of a finished product. For example, bakeries and restaurants that are restricted to take out orders only, have started selling raw ingredients to customers who have been unable to find the products they need on grocery store shelves. Just the other day, I personally purchased yeast and a 25 pound bag of flour from my local bakery because my grocery store had been out for weeks.
Weathering the Storm with Temperature Control
Most manufacturers have thorough supply chain time tables that help them communicate with suppliers, order and store raw materials, manage manufacturing timelines, ship finished products, and make or collect payments. Depending upon the industry, many manufacturers have had to throw out their old rule books and adapt to a business world that is constantly in flux. Let’s take a closer look at some practices that can help manufacturers protect their inventories and operations during this difficult time.
Increase Cold Storage
One of the most effective ways manufacturers can protect their business during this difficult time, is to increase their cold storage capacity. As spring turns into summer, hotter temperatures are already on their way. These temperatures threaten thermally sensitive raw materials and drastically reduce their shelf life and viability. The COVID-19 pandemic has made manufacturing input and output timelines extremely unpredictable. Adding extra cold storage capabilities to your facility will give you greater flexibility and protection.
For example, food suppliers work within a very delicate timeline to keep their products safe and viable from farm to table. Any disruption in the cold supply chain leads to costly waste. Bio and pharmaceutical companies adhere to even stricter cold storage and transportation guidelines.
According to the CBRE, an additional 75-100 million extra square feet of refrigeration and freezer storage will be needed nationwide to keep up with normal perishable food and pharmaceutical demands. The COVID-19 pandemic will greatly accelerate these cooling needs.
Greater Automation
Another important tool that manufacturers can use to weather the storm is increasing their use of automation. Most machinery and equipment require temperature controls to prevent overheating and breakdowns. Recent social distancing regulations and workforce reductions have shown how difficult it can be to keep things running smoothly with as few on-site workers as possible. Smart controllers offer manufacturers remote access to their temperature control equipment. By tapping into the Internet of Things (iOT), companies can remotely keep equipment running efficiently, protect temperature sensitive materials, and reduce the number of on-site workers.
Emergency Temperature Control Solutions From North Slope Chillers
During these uncertain times, it is important to find certain things you can depend on. Here at North Slope Chillers we are proud to offer efficient and expertly engineered cooling solutions that keep your operations up and running.
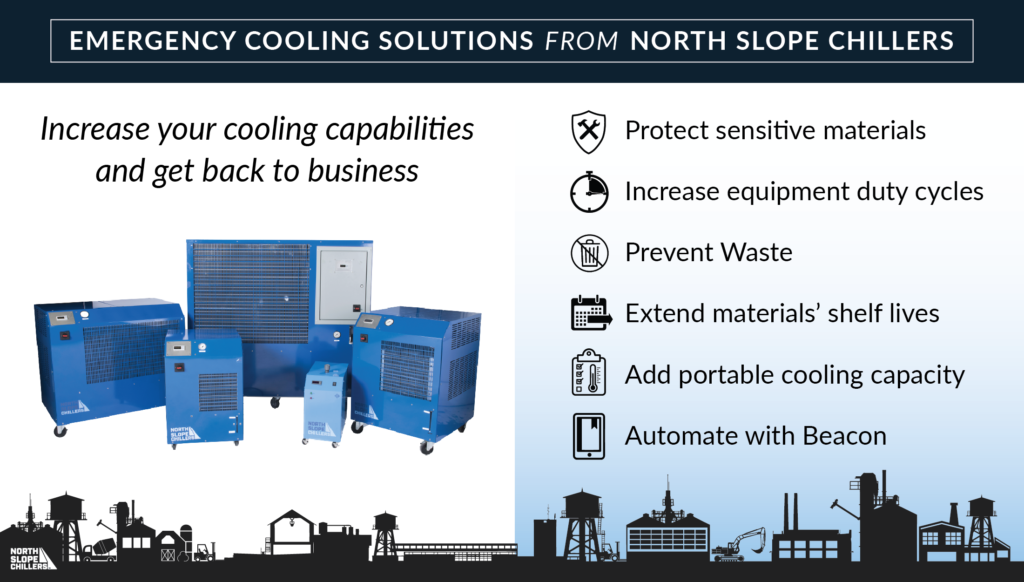
Our industrial chillers are portable and easy to install without disrupting your current setup. With expansive temperature ranges from 75°F all the way down to -112°F, you can be sure to find the exact cooling range for your needs. We can protect your temperature sensitive materials during supply chain disruptions, keep your equipment cool and running efficiently, and provide peace of mind during turbulent times.
In addition, with our Beacon smart controllers, we can streamline your temperature control needs and allow you remote access by putting cooling power right at your fingertips. With world class customization options available, you can be sure to find the perfect cooling solution for your needs. Contact us today at 866-826-2993 or [email protected] and find out how we can help you get back to business.