No Matter How You Slice It
Most industries have multiple options when it comes to cutting machinery. Between lasers, EDM (Electrical Discharge Machinery), plasma cutters, and water jet cutters we are spoiled for choice. Each cutting method has pros and cons and all have evolved into efficient and useful industrial tools. In the last 90 years, water jet cutters have become highly tuned machines capable of powerful and intricate results.
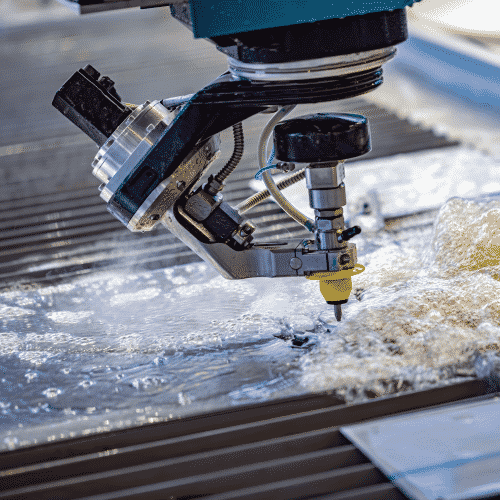
History of Water Jet Cutting
Innovative humans have found water a useful erosion tool for many ages. For example, ancient Roman miners used water for soft material excavations when mining underground. They would store water above a mine and flush the mining cavity to remove debris and expose what they were mining for. During the California gold rush in the 1850s, gold seekers used higher pressure water hoses to blast away at the Sierra Nevada Mountains. This hydraulic mining practice was discovered to be extremely damaging to the surrounding environment and has since mostly fallen out of practice.
However, the use of water jets to erode specific materials has continued in many applications. In the 1930s, a paper company in Wisconsin began using a highly focused water jet to cut paper. The technological advances spurred by World War II led scientists to begin to fine tune and increase the pressure and power of water jet cutters. Also in the 1930s, multiple developers worked on water jets with added pieces of abrasive materials to vastly increase their cutting power.
In 1956, an inventor in Luxembourg created a water jet that could cut out plastic shapes. 2 years later, North American Aviation began using an ultra high powered water jet cutter that reached 100,000 psi and could cut through hard materials. This water jet was proven to be too powerful for certain laminate materials, but its development was helpful in fine-tuning future models.
In 1962, an American chemical company named Union Carbide developed a 50,000 psi water jet that was able to cut a variety of hard materials like stone and metal. Over the next few decades, scientists refined water jet nozzles and equipment to make them more versatile, more efficient, and longer lasting.
Technology was pushed even further in the 1980s when researchers began using ice as an abrasive material to reduce the environmental impact of water jet waste.
Modern Water Jets
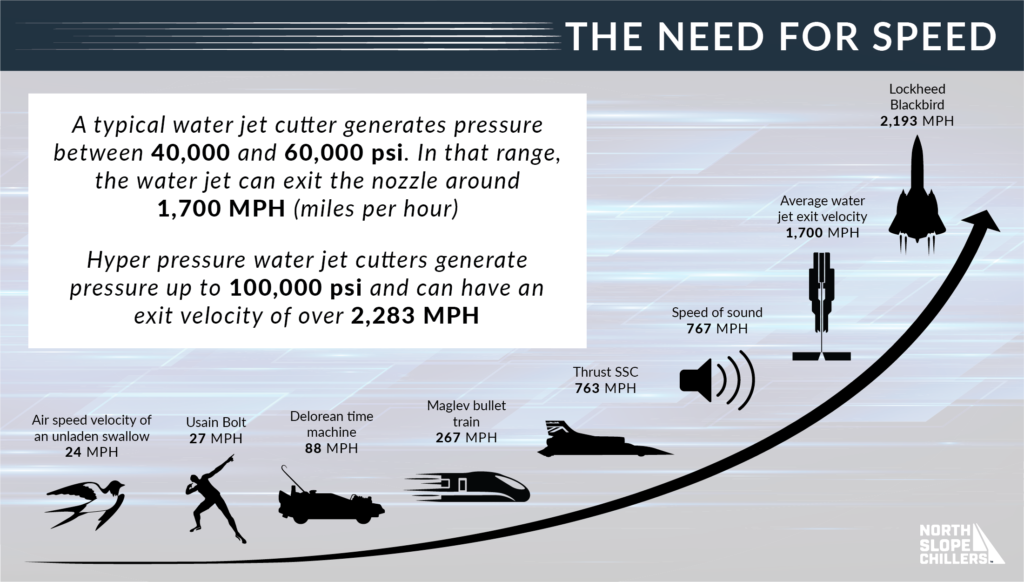
The automotive, aviation, and oil mining industries continued to drive the development and refinement of water jet cutters for many years. Today, water jet machines are highly versatile and can still be tuned for soft materials like paper and leather, and amplified for extremely high pressures and exit velocities. The average water jet nozzle generates 40,000-60,000 psi and the water exits the nozzle around 1,700 (mph) miles per hour. Hyper water jets can reach 100,000 psi and exit velocities of over 2,200 mph! Modern water jet machines range in size, power, and application and are used in many industries to provide them with heat and chemical free cutting for a huge range of materials.
How Does a Water Jet Cutter Work?
Pure vs. Abrasive
Water jet systems can either employ a pure stream of high pressure water or can contain added abrasive materials to increase its cutting power. Whether pure water or abrasive, the general concept is the same.
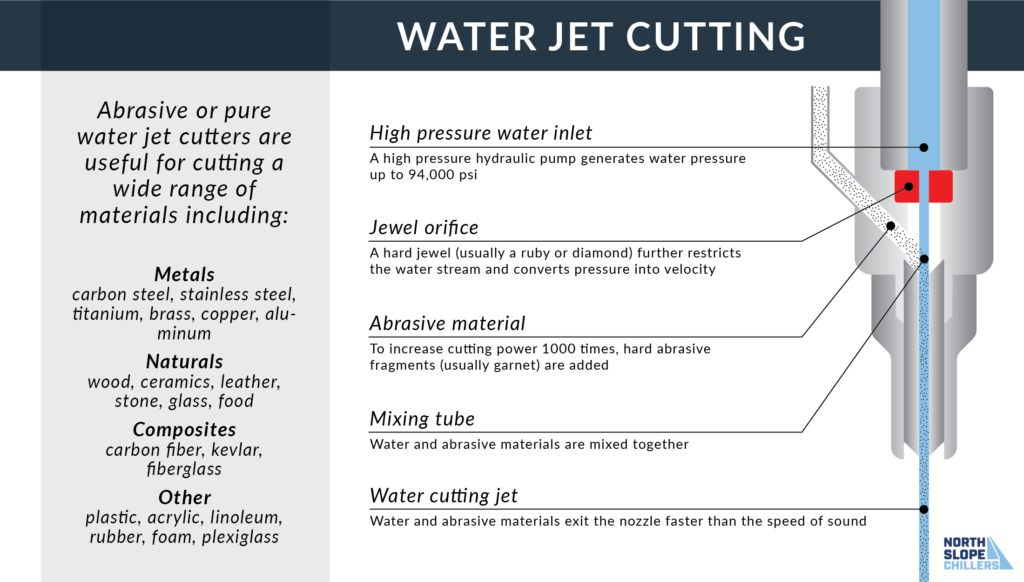
A high pressure hydraulic pump generates the water pressure levels needed for the cutting application. The highly pressurized water passes through a jewel orifice, usually a ruby (red corundum) or a diamond. The jewel must be as high as possible on the Moh’s hardness scale in order to protect it from eroding in the water stream. From here, the water flow is greatly restricted to a fine stream and all of the water pressure is converted into velocity. Some water jet nozzles emit water streams as thin as a human hair.
If needed, abrasive materials are now added to the water stream. The most common abrasive used is tiny powdered fragments of garnet, however silicon carbide, aluminum oxide, and even ice are sometimes used as well. The water jet leaves the nozzle faster than the speed of sound, and in some applications can reach over Mach 3!
Cryojets
Cryojets are water jet machines that use chilled water and ice particles as the abrasive substance. There are many advantages to using chilled water and ice as your cutting medium. Previously, the food industry could only use pure water jet machines because garnet and other abrasives are not safe to use on food.
Using an abrasive additive can increate a water jet’s cutting power 1000 times. By introducing ice particles as an option for abrasives, cryojets have innovatively created a safe and sanitary cutting solution.
Water Jet Cutting Applications
Aerospace
Water jet machinery and the aerospace industry go back a long way. For military or commercial aircraft, water jets cut interior cabin panels, engine components, metal and composite fiber body panels, rubber seals, and more.
Automotive
Water jets are convenient for cutting exterior and interior automotive components. Carbon fiber, fiberglass, seat foam, engine components, carpet, body panels, engine insulation…you name it, water jets can cut it.
Construction
Residential and commercial construction suppliers use water jet machines to cut a huge array of materials: stone, metal, tiles, glass, insulation and more.
Manufacturing
Looking into the broader manufacturing industry it is hard to find a task that a water jet cutter can’t perform: light textiles like fabric and paper, heavy duty metal parts, cable stripping, circuit boards, and even the special packaging used in shipping.
Food Processing
Pure water or cryojet cutters are used all the time for slitting and slicing frozen meat (including bone), vegetables, and a wide range of snacking goodies.
Water Jet Advantages
Operation
Water jet machines are typically simpler to set up and operate than EDM, plasma, and laser cutters. They also require less fine tuning and maintenance, and are much easier to repair and maintain. Their great versatility also makes them extremely valuable for any operation.
Heat and Chemical Free
Water jet machinery transfers very little heat to the cutting material. Small amounts of heat can be generated due to friction and the velocity at which the water jet hits the surface, but that heat is quickly dispersed into the water itself. This greatly reduces the chance of heat warping, melting, deformation, or discoloration as the materials are cut.
Because little to no heat is generated, water jets can be used on a wider range of sensitive materials like plastics, paper, leather, and even food. Water jets also do not emit harmful chemically loaded vapors as they cut, making it a safer work environment for personnel.
Water Jet Problems
Waste
Obviously water jet cutting is going to generate a large amount of waste water. This wastewater will also contain added abrasive powders, so it is not easily recycled. However, cryojets can use closed loop systems to recirculate the waste water to be used again and again.
Difficult Materials
Water jets are difficult to use on materials with empty spaces or voids such as tubing or honeycombed materials. Water jets can sometimes bend, taper, and change shape as they interact with the cutting material. Some manufacturers have engineered solutions to some of these problems, but it is still a possibility.
Hydraulic Pump Overheating
A water jet machine is only as powerful as its hydraulic pump allows. In most cases, a hydraulic pump should not critically overheat unless something is malfunctioning. However, high seasonal ambient temperatures can also cause hydraulic pump distress and reduce the duty cycle of your water jet machine. Additional process cooling may be necessary if you plan to use your water jet during the summer months.
North Slope Chiller Water Jet Solutions
Here at North Slope Chillers, we specialize in portable process cooling solutions that won’t interfere with your current setup. We can keep your machinery operating within safe temperatures, fluid reservoirs chilled, and provide custom chilling solutions for problems you never even anticipated. Our expert engineers can quickly create the exact cooling range and setup that would be beneficial for your operation.
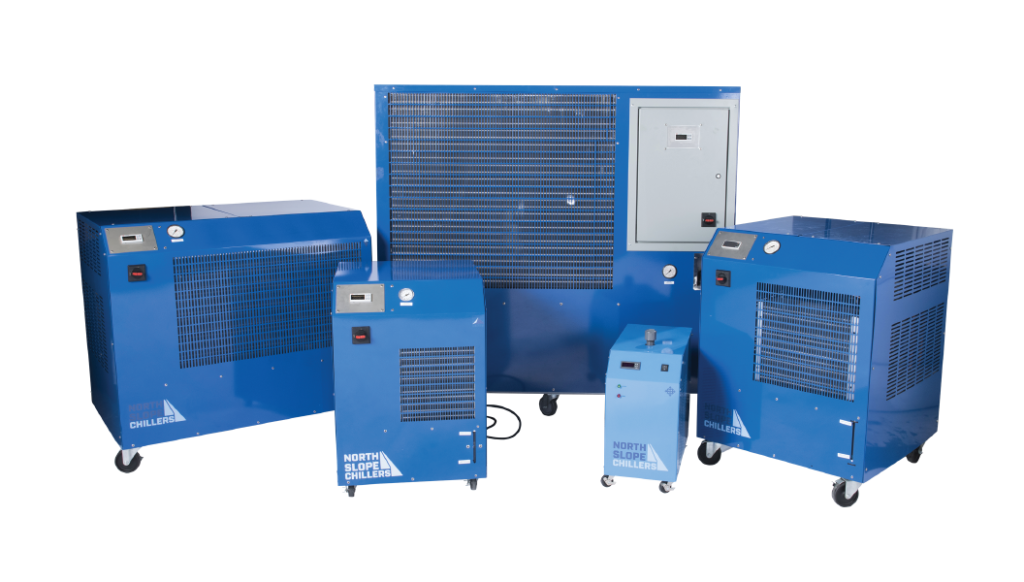
(866) 826-2993 [email protected]