What’s in a name?
Think you’ve never heard of a recirculating chiller before? Think again.
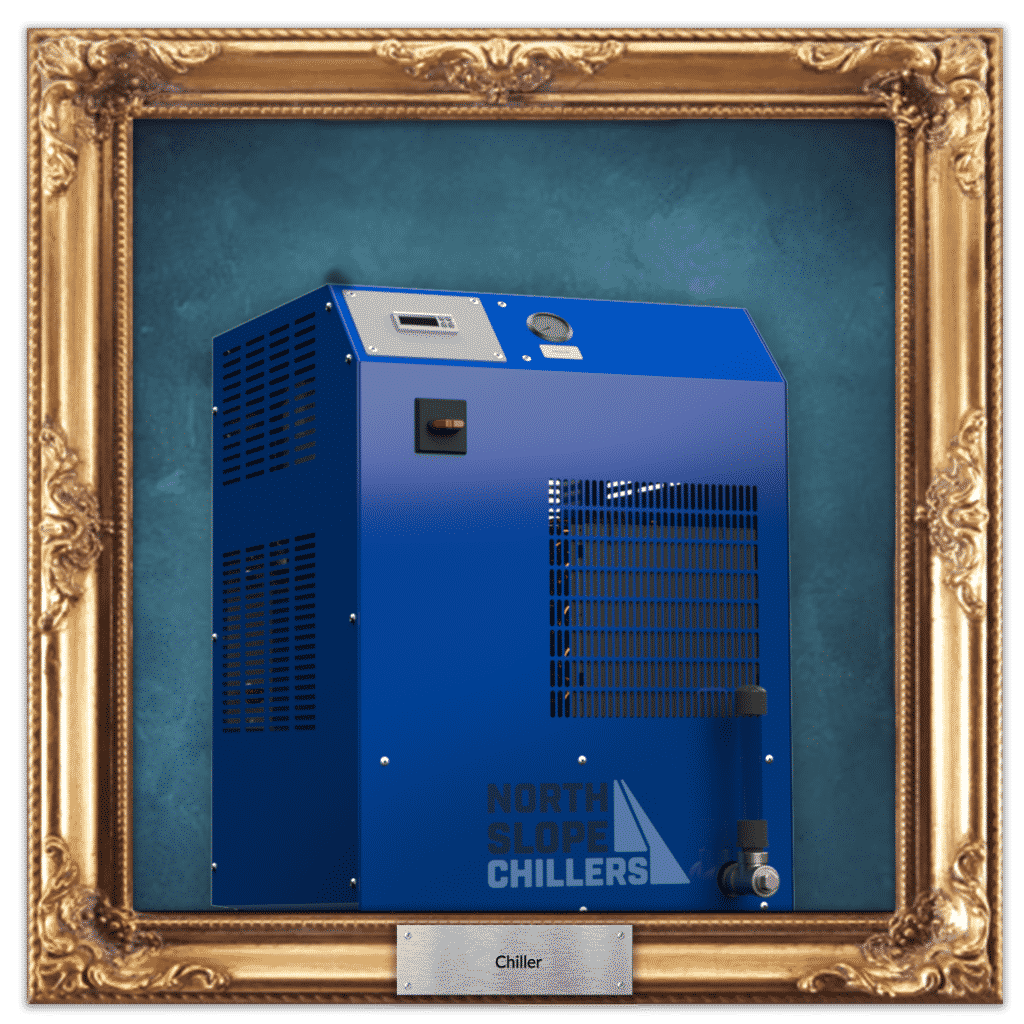
Chiller: You Know What It Is
When we think of industrial cooling equipment, the word that most often comes to mind is “chiller.” That’s because chiller is the term most often used in any industry when referring to cooling equipment.
Known By Another Name
Technically, these units are called recirculating chillers, aptly named for their ability to circulate liquids through a cooling system while drawing heat away from temperature-sensitive materials. Recirculating chillers come in a variety of shapes and sizes, suiting the specific industries they serve. From hydroponics to plastics, cannabis to dairy, and lasers to 3D printing, recirculating chillers are an important part of manufacturing everywhere.
Did you know that chillers originated in German breweries? Check out our article on how to keep beer cold to learn about how and why recirculating chillers came into existence.