How Low Can You Go?
Our modern lives, as we know them, would be very different without process cooling. Many of the products we use, buy, wear, and eat, rely heavily on precise temperature control at different stages of their manufacturing and transportation processes. But what do manufacturers do when their products require exposure to extreme temperature environments? Let’s take a closer look at ultra low-temperature process cooling, who needs it, and why.

Why Go So Low?
There are many reasons why certain industries need process cooling equipment to reach ultra-low temperatures. One of the most common uses of ultra-low temp chilling is for durability testing.
Durability Testing For Extreme Environments
Take a look around you. As most of us sit in our comfortably climate controlled homes, offices, and vehicles, it can be hard to imagine how the products around us would react to extremely cold temperatures. At what point would they stop working…crack…explode…rupture? Most of the items around you would never naturally reach those temperatures, so there is little reason to worry. Everyday items undergo typical durability testing to make sure they can operate safely and efficiently in a wide range of seasonal environments.
However, materials and devices that are intended to operate in the upper atmosphere, deep ocean, or outer space must undergo more rigorous testing. In order to be prepared for anything mother nature can throw at them, every piece of equipment, protective gear, machinery, electronics, and other supplies need to be thoroughly tested before they can be safely used in such an environment.
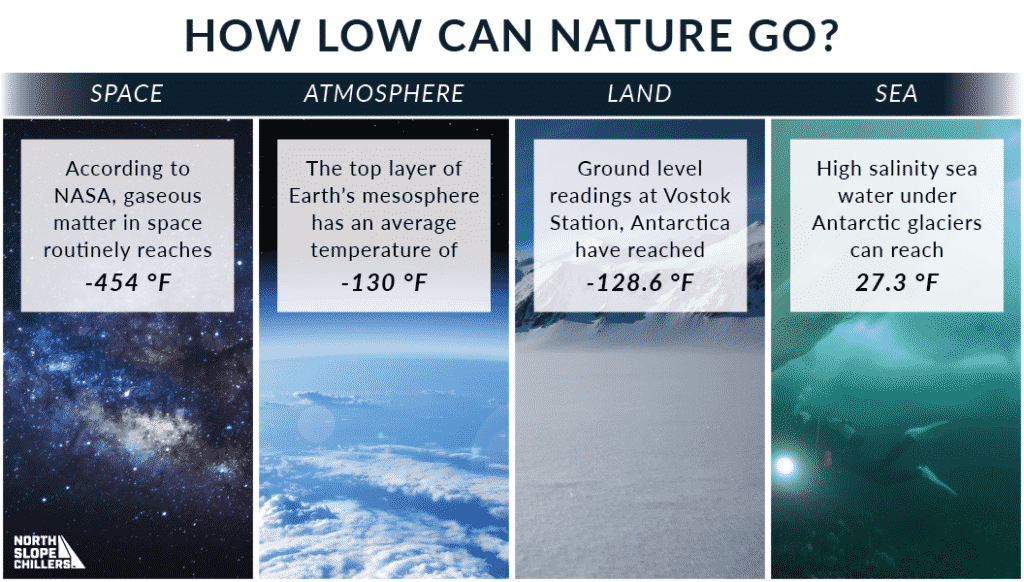
Land
The lowest temperature ever recorded at Earth’s ground level occurred on July 21, 1983. The Soviet run Vostok Station in Antarctica recorded a temperature reading of -128.6° F (-89.2° C). More recently, satellites have detected even lower readings (some as low as -144° F), but the 1983 record is still recognized as the most accurate reading from the ground level.
Sea
Similarly, the coldest seawater temperature was also recorded in Antarctica. A super salinated stream of seawater running under an Antarctic glacier measured in at 27.3° F. The high salt content allowed the water to reach sub-freezing temperatures and still remain liquid.
Atmosphere
Another natural extreme temperature environment exists above us at all times. The Earth’s atmosphere is comprised of multiple layers, and each has different environmental conditions. The mesosphere is the layer that extends from 31-53 miles above the Earth’s surface. The top of the mesosphere (aka the mesopause) is the coldest section of our atmosphere and has an average temperature of -130° F.
Space
For the most extreme temperatures, we have to look beyond our home planet. According to NASA, gaseous matter out in space routinely drops to -454° F. Because of the extremely cold conditions in space, astronauts will soon be able to conduct quantum cooling experiments in the Cold Atom Laboratory (CAL) on the International Space Station (ISS). There, astronauts will be able to use quantum process cooling to chill atoms well below the average temperature of deep space, boldly going where no thermometer has gone before.
Cryogenics
Another common need for ultra-low temperature process cooling lies in the vast field of cryogenics. Broadly speaking, cryogenics is the study of ultra-low temperatures and how matter behaves at those temperatures. According to the Encyclopedia Britannica, cryogenic temperatures range from -238°F all the way down to -460°F or absolute zero. Absolute zero is theoretically the point where molecular motion is as close as it can get to stopping completely. Over the years, many different cryogenic sub-studies have evolved in our modern world.
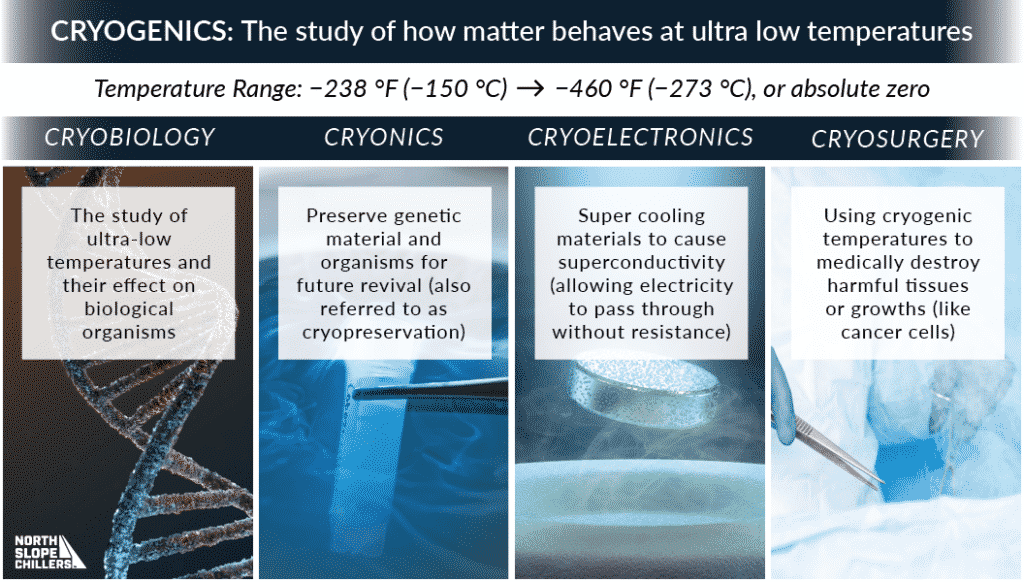
Cryobiology – studying the effect of ultra-low temperatures on organisms
Cryonics/Cryoconservation/Cryopreservation – conserving genetic material and organisms for future revival
Cryoelectronics – the study of electricity at ultra-low temperatures
Cryosurgery – using cryogenic temperatures to medically destroy harmful tissues or growths
Materials behave very differently when exposed to cryogenic temperatures. Some, like rubber, become so brittle they are easily broken down. Others, like ceramics and some metals, become superconductive and allow electricity to flow through them with zero resistance.
What Industries Use Ultra-Low Temperatures?
The field of cryogenic and ultra-low temperature process cooling is expanding every year. As we continue to find new ways of utilizing this technology, the possibilities seem endless. Let’s look at some specific examples of industrial uses for ultra-low temperature process cooling.
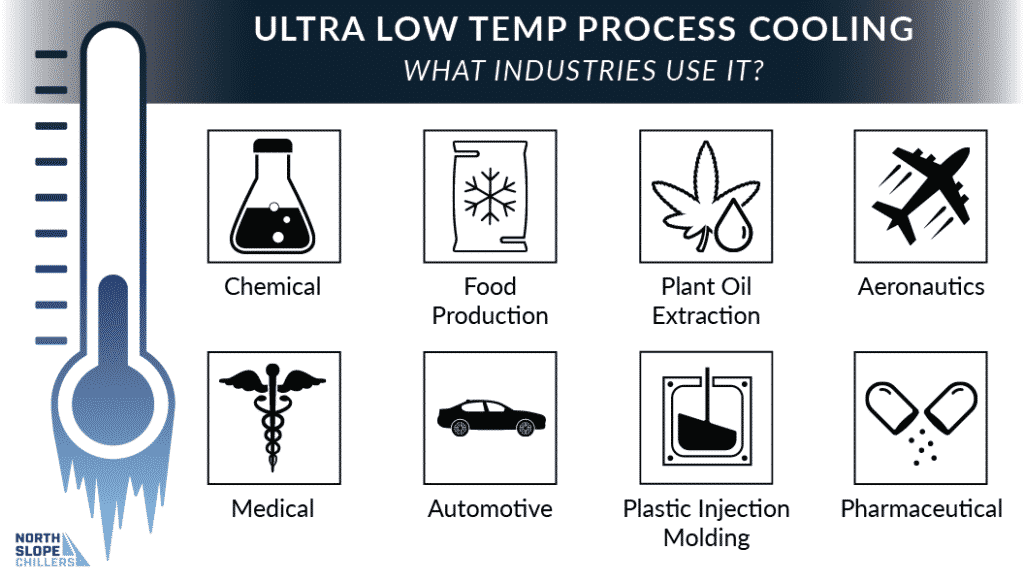
Aerospace
The aerospace industry must rigorously test every component used in modern aircraft for its ability to withstand extreme temperature changes. Ultra-low temperatures can increase wear and in compromise the structural integrity of many kinds of materials. These aeronautic materials undergo what is known as cryogenic tempering to increase their durability. They are exposed to strategic high and ultra-low temperatures during fabrication so their microstructure becomes more stable, durable, and long lasting. Cryogenic processing is used to improve the performance and strength of engine components, turbine blades, seals, brake lines, and more.
Pharmaceuticals/Medical
Medical and pharmaceutical laboratories use ultra-low temperature freezers and storage rooms to preserve important samples. These can include: bone marrow, blood, stem cells, vaccines, DNA and RNA, Sperm, Eggs, Embryos, and more. Many of these samples are extremely valuable and some are irreplaceable. Ultra-low temperature storage and transportation is absolutely crucial to protect the viability of delicate lab products.
Pharmaceutical companies also use ultra-low temps for the lyophilization (freeze-drying) process. Lab samples are inserted into a special ultra-cold vacuum chamber that freezes and removes moisture simultaneously.
In addition, some medical devices, like MRI machines (which require cryogenic cooling temps of -400° F) need ultra-low temperature process cooling in order to operate safely.
Food Service
If you have ever purchased frozen seafood in a landlocked state, then your taste buds have benefitted from ultra-low temperature process cooling. Commonly referred to as “flash freezing”, food products can be frozen so quickly, they don’t expand or lose taste or nutritional value. Flash freezing also preserves natural flavors so your food still tastes fresh and delicious.
Automotive
Similar to the aerospace industry, the automotive industry tests structural and engine components for usability in extreme temperatures. Testing a car in ultra-low temperatures allows car manufacturers to see if fluids and batteries hold up, electronics still function, how quickly the engine and cabin heat up, and to what degree the vehicle is still operable.
Defense
Civilians like us will never know all the ways the defense industry uses ultra-low and cryogenic temperatures. However, looking closely at the private sector we can see many ways the defense industry can benefit from ultra-low process cooling. As mentioned above, aerospace engineers subject every material used on an aircraft to thorough temperature testing. Ultra-low temperatures are also useful for storing and transporting flammables and combustible materials safely. Cryogenic tempering is also used on a wide variety of metals (including on firearms) to strengthen their microstructure and increase durability.
Chemical
Storing and transporting temperature sensitive chemicals can be extremely dangerous. Many flammable and combustible materials require ultra-low temperature solutions in order to meet hazardous location safety certifications.
Plant Oil Extraction
Extracting highly pure oils out of plant matter involves some ultra cold temperatures. Some companies use CO2 extraction methods that use carbon dioxide which is chilled below -69° F. Some companies also use ultra-low temperatures (-20°F) to remove natural waxes from their extracts. These extraction methods produce high concentration oils that are very valuable. In recent years, the production and use of essential oils, especially CBD oil, has grown into a very lucrative industry.
Plastics
Plastic injection molding is a highly efficient plastic manufacturing method that greatly reduces waste material. Special thermoplastics (such as ABS and Polyethylene) are heated, injected into a mold and then quickly chilled before they are released from the mold. Molding plastics at high temperatures creates a nice glossy finish and makes the finished plastic more heat resistant. Rapidly chilling then makes the plastic stronger and more impact resistant.
North Slope Chillers Ultra-Low Temperature Solutions
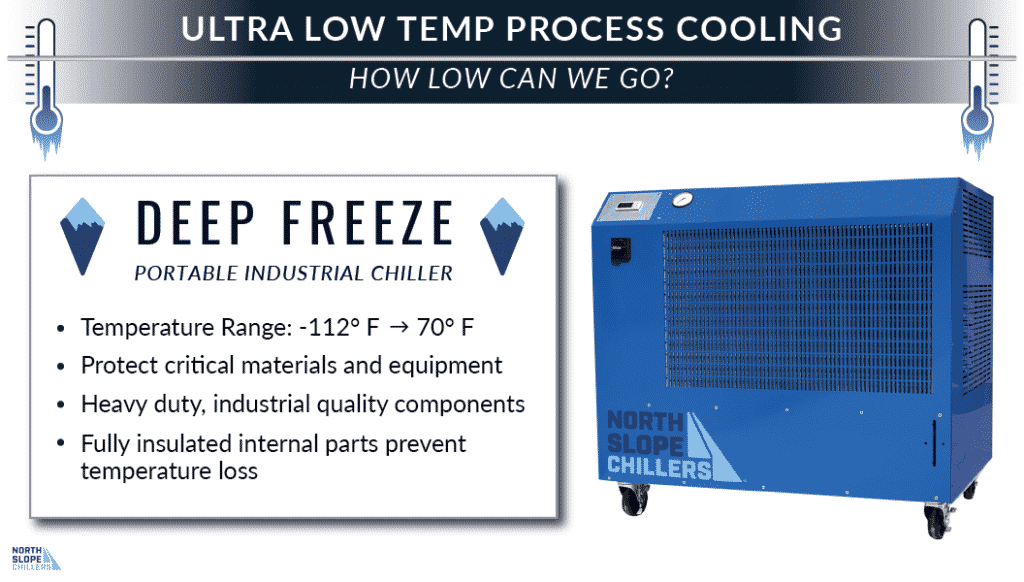
Here at North Slope Chillers, we specialize in portable and powerful industrial process cooling. Our Deep Freeze line features a wide temperature range from -112° F to 70° F. With fully insulated interior components, Deep Freeze operates efficiently with little thermal loss. If you need a liquid cooling system that is both reliable and as cold as it gets, look to Deep Freeze. Contact us today to find the perfect ultra-low temperature solutions for your needs at (866) 826-2993 or [email protected]