Plastic Injection Molding
Plastic injection molding is a crucial manufacturing process in today’s modern world. The ability to mass produce identical plastic components further drives innovation and industrial progress every year. The goals of successful plastic manufacturing are precision, repeatability, and speed. These same goals should be applied to cooling plastic as well.
The cooling process can consume at least 80% of the overall plastic manufacturing time. That means, by applying an efficient industrial cooler to the injection molding process, you can greatly reduce the amount of time spent on each batch. But where does one begin the process of looking for an injection molding chiller? Let’s take a closer look.
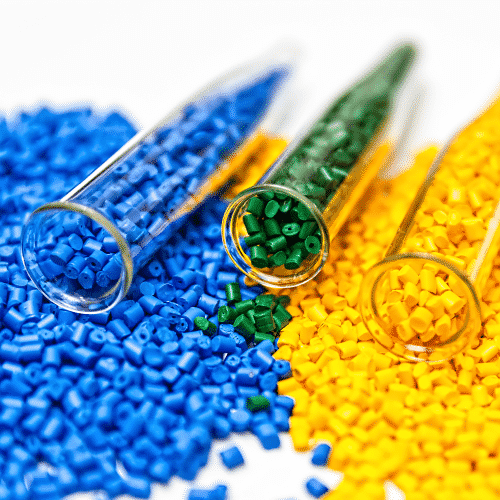
What to Know When Selecting an Injection Molding Chiller
Cooling molten plastic is a complex science with many variables. However, there are certain questions that will guide you when selecting an injection molding chiller.
What are my melting points?
Plastic melting temperatures vary greatly depending upon the type of plastic required for the job. Knowing the molten temperature of your plastic in the nozzle is the first step in selecting a chiller that will cool it before ejection. Here are some common plastic melting points and ranges:
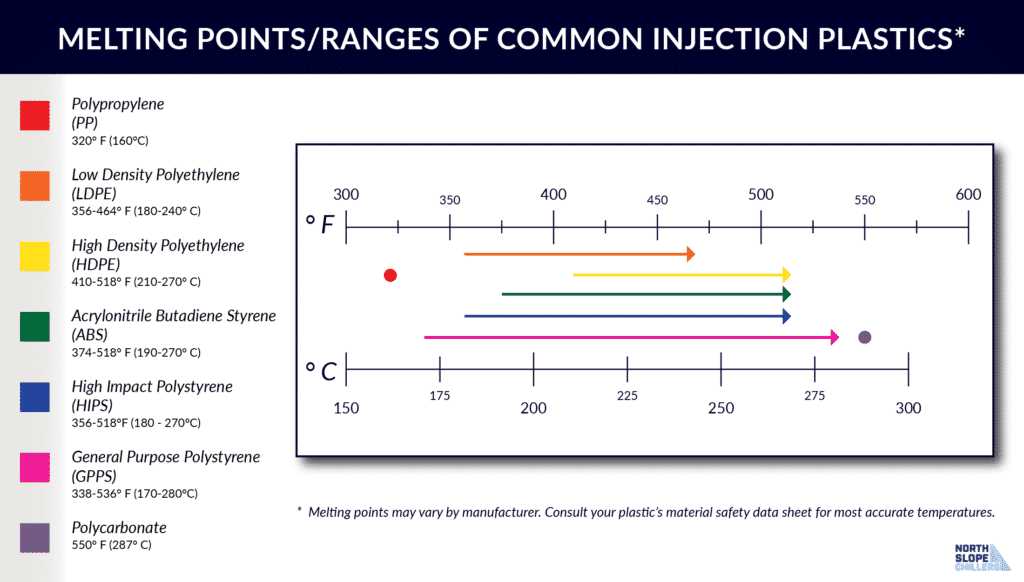
- Polypropylene (PP): 320° F (160° C)
- Low Density Polyethylene (LDPE): 356-464° F (180-240° C)
- High Density Polyethylene (HDPE): 410-518° F (210-270° C)
- Acrylonitrile Butadiene Styrene (ABS): 374- 518° F (190-270° C)
- High Impact Polystyrene (HIPS): 356-518° F (180 – 270° C)
- General Purpose Polystyrene (GPPS): 338-536° F (170-280° C)
- Polyoxymethylene: (POM): 347° F (175° C)
- Acetal: 356-410° F (180-210° C)
- Acrylic: 428-482° F (220-250° C)
- Thermoplastic Polyurethane (TPU): 374-428° F (190-220° C)
- Polycarbonate: 550° F (287° C)
These melting points and ranges may vary depending upon the plastic manufacturer. Be sure to thoroughly research your plastic’s heating needs so you know what your goal temperatures are.
What are my HDTs?
Next, research the Heat Distortion Temperature (HDT) of your plastic selection. Plastic components need to be chilled below their HDT in order to avoid deformation when ejected from the mold. HDTs differ depending upon the plastic’s composition, the molten density, and the pressure in the mold. Again, consult your plastics manufacturer to ensure you know your chosen material’s temperature ranges.
What is my desired mold temperature?
Proper plastic chilling is more involved than just cooling as quickly as possible…it involves carefully hitting temperature targets. Your plastic manufacturer will also be able to provide the ideal mold temperature for your plastic selection. Achieving your mold temperature allows your plastics to cool and crystallize properly in the mold. Proper crystallization prevents cavity formation, stress cracking, creeping and seeping plastic, and other deformities.
How much space do I have?
Injection molding equipment can take up a large amount of space on the factory floor. Because chilling equipment can greatly add to that footprint, you will need to know how much room you have to work with. Water cooled chillers use a cooling tower that takes up more space than air cooled chillers, so select an industrial chiller that will meet your space requirements.
How much cooling power do I need?
Chiller sizes are traditionally listed according to “tons.” Tons does not refer to the actual weight of the chiller, but instead is a historical reference to a time when blocks of ice were harvested for cooling. Just like engines are still measured according to “horsepower”, the term “tons of refrigeration” stuck around. 1 ton of cooling power = 12,000 btus per hour.
Cooling power for your injection mold
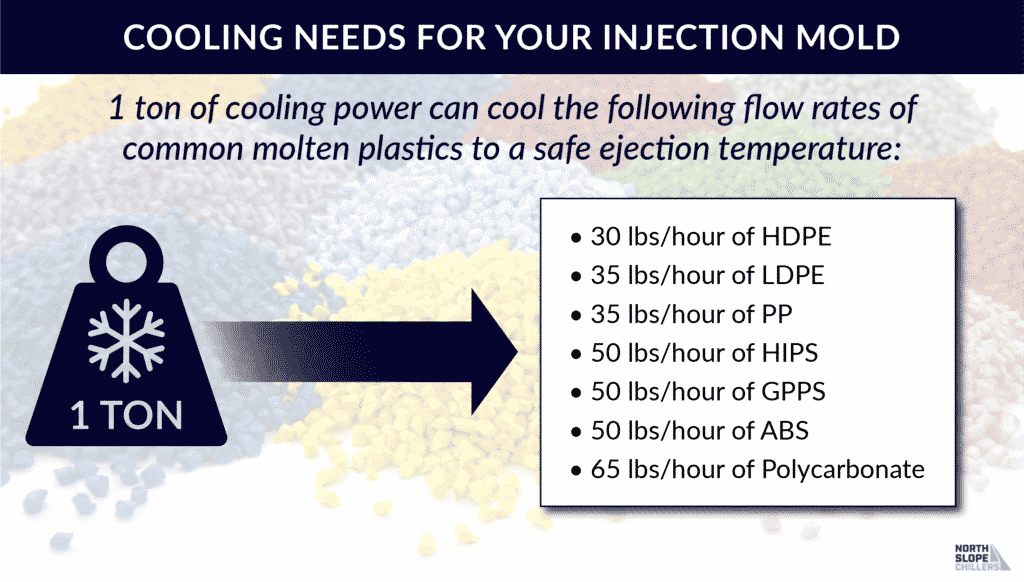
As a general rule of thumb, 1 ton of cooling power is sufficient to cool the following flow rates of molten plastics to a safe ejection temperature:
- 30 lbs/hour of HDPE
- 35 lbs/hour of LDPE
- 35 lbs/hour of PP
- 50 lbs/hour of HIPS and GPPS
- 50 lbs/hour of ABS
- 65 lbs/hour of Polycarbonate
Cooling power for additional equipment
In most cases, the injection mold will not be the only piece of equipment in need of cooling. There are other pieces of auxiliary equipment that require process cooling in order to extend your machine’s duty cycle.
- Hydraulic motor (additional .1 tons of cooling per horsepower)
- Feed Throat (additional .5 tons of cooling)
- Thermolator (additional .2 ton per pump horsepower)
- Hot Runners (additional .15 ton cooling per kilowatt hour)
- Dryer Aftercooler (consult your dryer manufacturer to determine how much additional cooling is required)
What Should An Injection Molding Chiller Have?
Portability
Portable industrial chillers give you a greater amount of flexibility and save valuable floor space.
Quiet Compressors
Anytime you install additional equipment on an injection mold factory floor, you increase the operational noise in your facility. Your chilling unit should be powered by compressors that operate efficiently but quietly. In general, chillers with reciprocating compressors are much louder than centrifugal, scroll, or screw compressors.
Flexible Temperature Ranges
The plastic cooling process will vary depending upon many factors: size and thickness of the plastic part being made, type of plastic, etc. Installing an industrial chiller with the flexibility to hit a range of temperatures broadens your manufacturing capabilities.
Recirculation
Save money and protect our precious resources by installing a recirculating chiller. Recirculation greatly reduces water consumption and will help you save on utility bills in the future.
Precise Temperature Controls
Molten plastic can behave in unpredictable ways unless you hit precise temperature targets during the heating and cooling process. Smart thermostatic controllers give you peace of mind with greater access to cooling time frames and temperature ranges.
Customization
Some injection molding operations require specific components and specifications to meet their cooling needs.
For example, plastic products made for the food and beverage, bio and pharmaceutical, industries must meet FDA standards for food-grade materials. Facilities that manufacture these plastics must maintain clean-room conditions and all equipment must be easy to wipe down and sanitize. Injection mold chillers for these facilities should contain corrosion resistant components. They should also be contained inside easy-to-clean enclosures to help maintain factory cleanliness.
Efficient Cooling Fluids
Injection mold chillers must produce cooling power that is able to penetrate through the mold and efficiently remove heat from the plastic. Fluids such as water/glycol mixes remove waste heat more efficiently than water alone.
North Slope Chillers Injection Mold Chilling Solutions
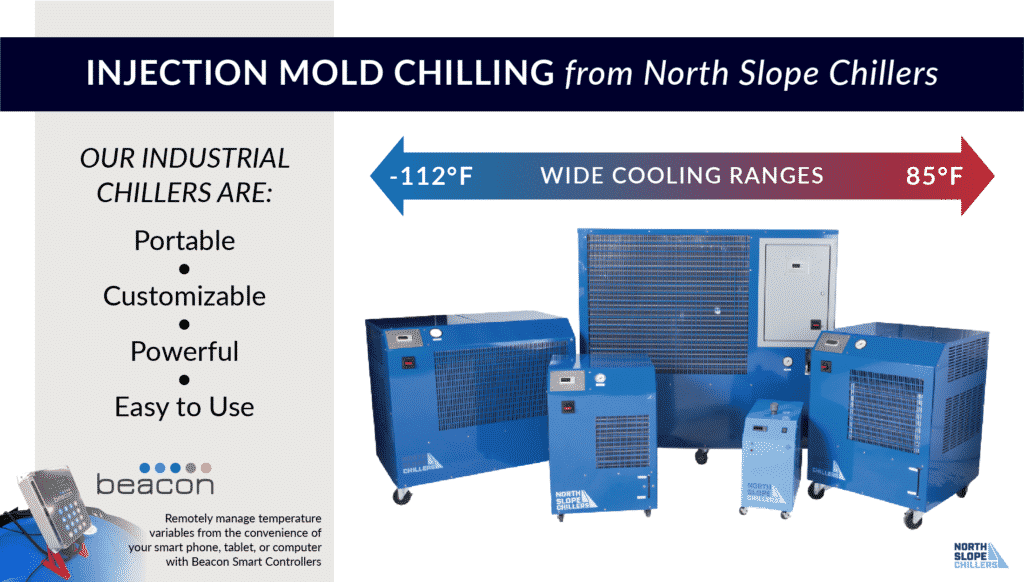
At North Slope Chillers, we are proud to offer portable and powerful injection mold chilling solutions. Easy to install and use, our chillers come with a wide range of cooling temperatures. In addition, our customization process is the fastest on the market and can provide you with the exact specifications you require.
Contact us to find the right injection mold cooling solution for your needs:
(866) 826-2993 [email protected]