The Perfect Fit
We cannot overstate the importance of selecting a correctly sized chiller. Undersized chillers won’t correctly cool your process equipment or materials. Oversized chillers will work just fine, but why pay more than you need to? When you select a chiller of the proper size, you can rely on several years of efficient cooling. Let’s explore the different parameters one needs to find the perfect chiller size.
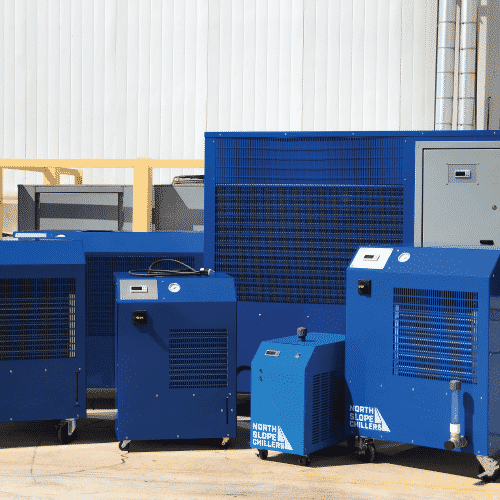
Tonnage Explained
A Historical Custom
Why are chiller sizes listed according to tons? Well, the answer lies in the cooling practices of yesteryear. Before the age of electronic air conditioners, here in North America especially, blocks of ice were harvested from frozen lakes and rivers and used to cool homes during the summertime. 1 ton of cooling power was the amount of heat transfer needed to melt 1 ton of ice blocks in a 24 hour period. As cooling technology advanced, we began to shift from stored ice to mechanical chilling. In today’s measurements, 1 ton of cooling power = 12,000 btus per hour. Just like we still measure engines according to “horsepower”, the historical practice of using “tons of refrigeration” stuck around.
Pumps and Compressors

A chiller works by using transferring heat between 2 different circuits: the fluid circuit and the refrigeration circuit. The fluid circuit moves unwanted heat into a process fluid, and the refrigeration circuit takes that unwanted heat and disperses it into the ambient air. Both circuits work together continuously to remove excess heat. The fluid circuits uses a pump to keep things flowing, and the refrigeration circuit uses a compressor. The fluid pump and the compressor are the dual engines that keep the chiller running.
Great care is used when selecting the type of pump and compressor used in our chillers. Power, flow rate, efficiency, durability, and noise levels are all taken into consideration for every chiller we offer.
Volts Vs. Amps
Units of electricity can be measured in a few different ways. 2 of the most basic electrical units are used to measure the voltage (volts) and the current (amps). An easy way to understand the difference is to compare electrical flow to water flow. Imagine an electrical wire as a pipe. The voltage (volts) would be the same as measuring the water pressure, and the current (amps) would equal the amount of water in the pipe.
The Formula
Regardless of what you are cooling, this formula will determine your needed chiller size. Before jumping in, identify the following variables:
- Incoming water temperature
- Required chilled water temperature
- Flow rate
To illustrate how this formula works, let’s say we need to cool 4 GPM (gallons per minute) from 85 °F to 75 °F. This makes our incoming water temperature 85 °F, the required chilled water temperature 75 °F and the flow rate 4 GPM.
Step One: Calculate Temperature Differential (ΔT°F)
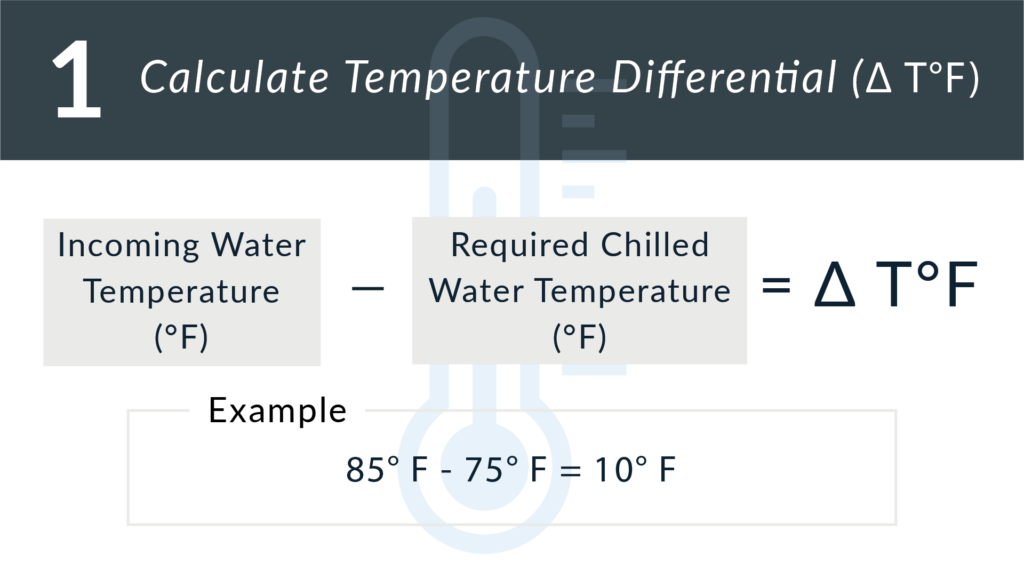
Step Two: Calculate BTU/hr.
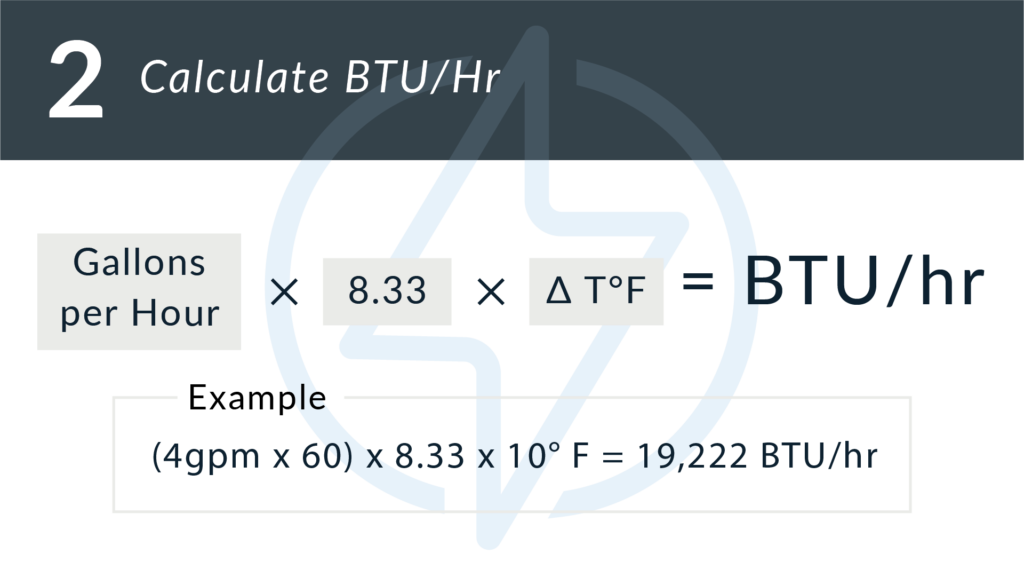
Step Three: Calculate tons of cooling capacity
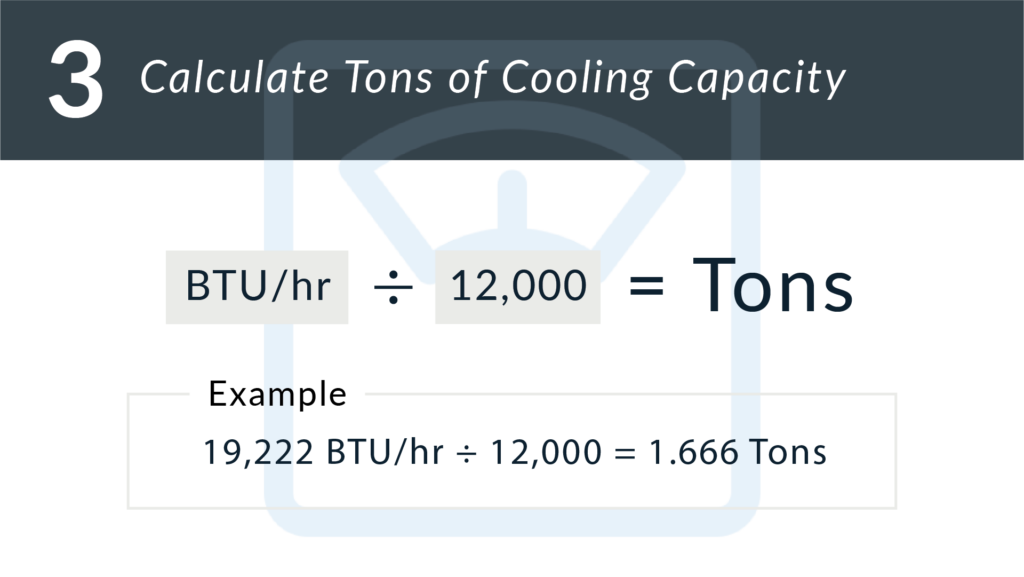
Step Four: Oversize the chiller by 20%
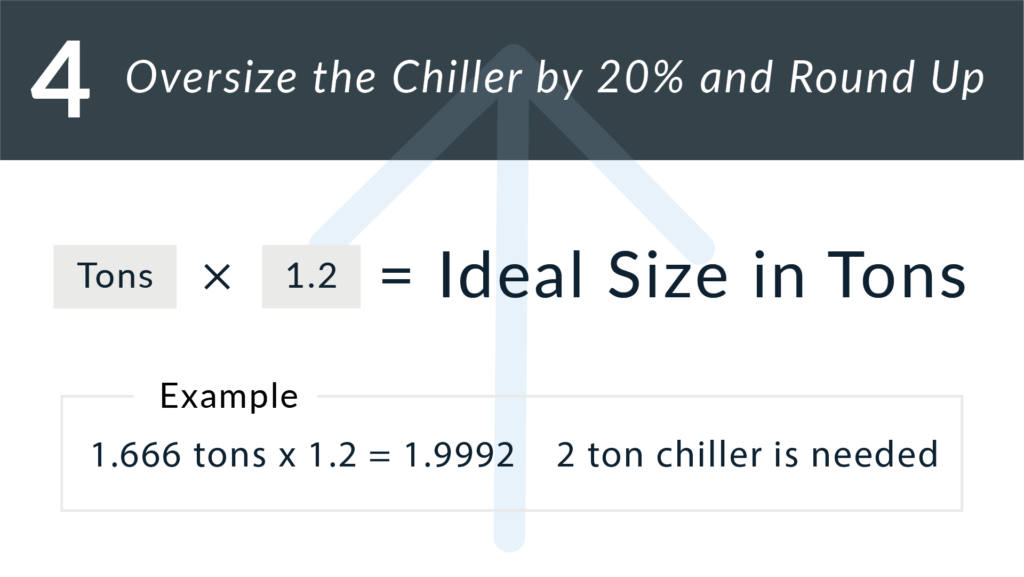
Most likely, your “Ideal Size in Tons” is not going to come out to an even 1 ton, 5 tons, 20 tons, etc. Rounding up will also help you be prepared for any unforeseen heat sources that are present in your setup.
We hope this was helpful! Of course, if you have any questions or would like us to size your chiller for you, please give us a call at (866) 826-2993 or email [email protected]