Temperature control is a vital part of nearly every step in the beer-making process. From boiling to fermentation, all brewers have to stay in charge of heat.
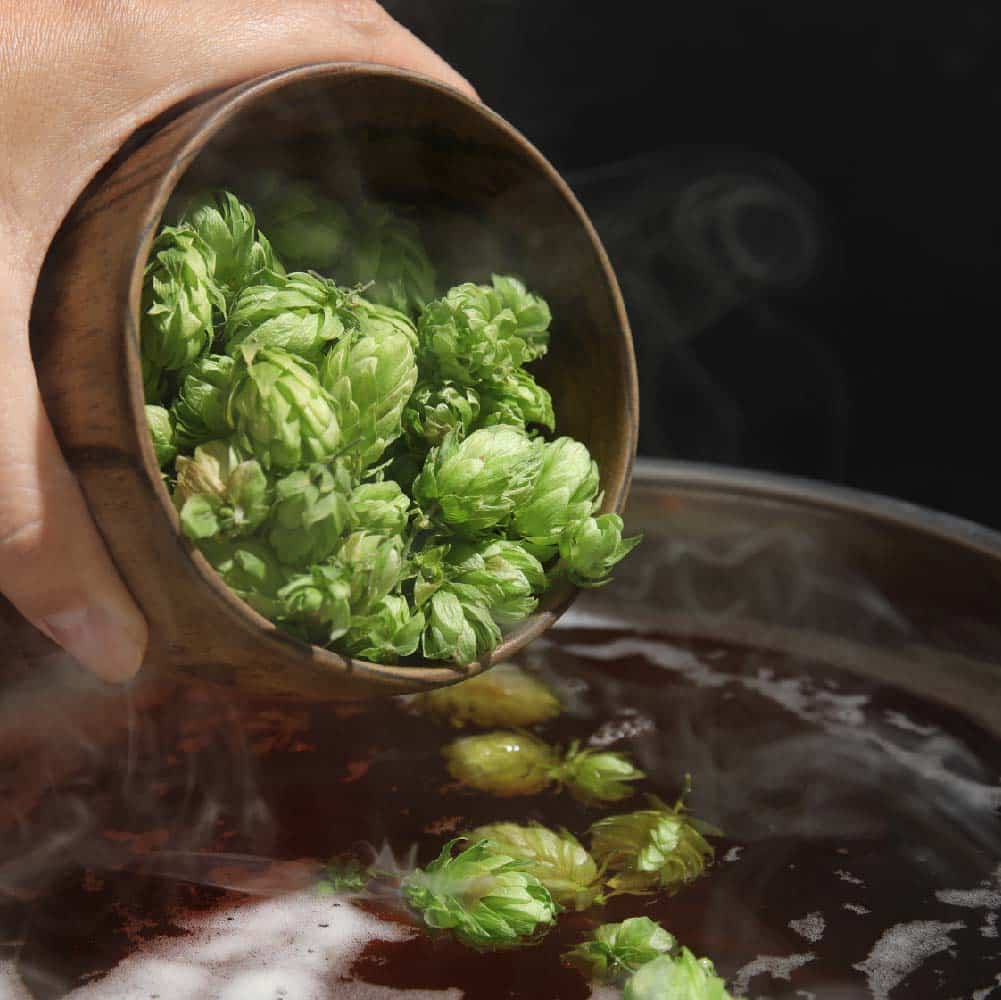
During the lautering phase of brewing, temperature control plays a critical role in ensuring flavors are developed correctly. Without control, beer flavors can vary and develop unwanted tastes and textures.
Lautering is broken up into three steps:
Mashout
Mashout is the term used to describe the heating of mash. Doing so helps liquify the mash and stop the fermentation of starches within the mash. This is where temperatures get precise. Optimum temperature of mashout is 170° F, which kills off bacteria that was formerly assisting the fermentation process.
Recirculation
Once wort liquifies, it’s best to recirculate it through the mash repeatedly. The mash acts as a filter, catching small pieces of grain and other debris leftover from earlier phases of the brewing process. Recirculation is best performed by draining wort water out from the bottom of the mash and spraying it back over the top.
Sparging
Sparging is the most delicate part of lautering because any errors will significantly impact the flavors of the brew, especially the bitterness levels. Water is sprinkled on top of the grain to extract sugars that will be vital to beer taste.
There are two methods of sparging, English and German. In English sparging, the wort is completely drained from the mash. Once the wort is removed, water is added to the mash. This time, the water is held at exactly 169° F. Eventually, the water can be drained and either be added to the wort or be used as its own light brew.
In German sparging, water is added at the same rate as the wort is being drained from the mash. The main difference between English and German sparging is that German sparging generally results in a larger quantity of beer.
Cold Control
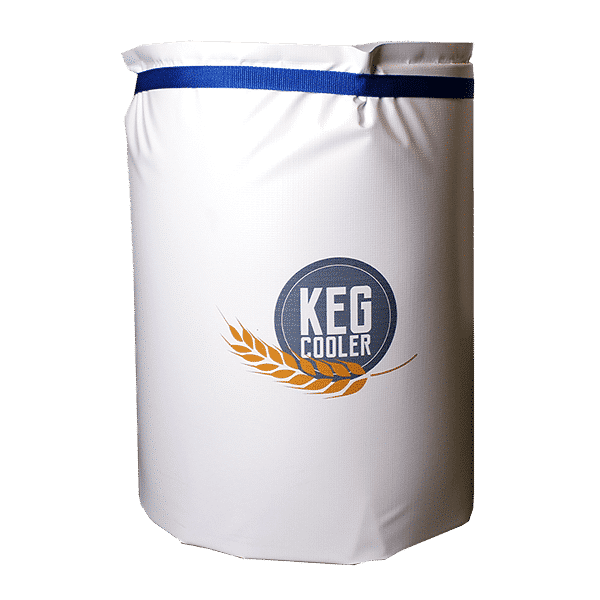
Using temperature control equipment during lautering is important to protect these sensitive chemical changes. North Slope Chillers specializes in equipment brewers need to stay in command of their brew. Using Keg Coolers and Beacon Control technology takes the pressure off brewers as they move forward into the next part of beer-making, leading to a brew that drinkers can’t help but drain to the last drop.
Contact North Slope Chillers to find the right temperature control equipment for your brewing needs at (866) 826-2993 or [email protected].