If you work with industrial machinery, you might use a process chiller system to keep your machines from overheating. They can be very effective in keeping things at optimal temperatures, but how does a chiller work? Knowing how process chillers work can be helpful in choosing the best system to meet your needs.
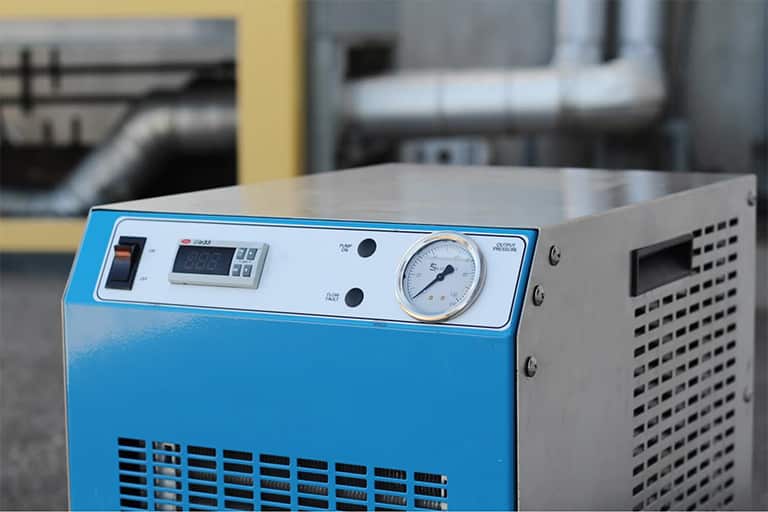
How a Chiller Works
To put it simply, industrial chillers cool process fluids. Process fluids (typically water or a water/glycol mix) are used to cool machinery, equipment, food, etc. The process fluid absorbs heat from what is being cooled and then goes through the chiller where the heat is removed from the fluid and transferred to the ambient air.
Two Circuits
Industrial water or glycol chiller systems contain two main circuits: a refrigeration circuit and a fluid circuit. The refrigeration circuit is made up of four components: the compressor, the condenser, the expansion valve and the evaporator. The refrigeration circuit removes heat from the process fluid. The fluid circuit is typically comprised of a fluid reservoir, a pump, filters, and a heat exchanger. The fluid circuit carries the process fluid around the object being cooled.
The Refrigeration Cycle Step by Step – Chiller Diagram

The refrigeration circuit is the most technical part of how a chiller works.The refrigeration cycle uses the principles of thermodynamics to efficiently move heat from one area to another. In the case of chillers, heat is taken from the fluid being chilled and transferred to the ambient air.
- The Compressor
The refrigeration cycle begins with the compressor. The compressor takes low-pressure low-temperature refrigerant in gas form and compresses it into a high-pressure high-temperature gas.
- The Condenser
This gas then flows through coils in the condenser. While in the condenser, air or water will flow over the coils and remove heat from the refrigerant. As the refrigerant loses heat it will begin to condense until all of the gas has condensed into a liquid.
- The Expansion Valve
After leaving the condenser, the liquid goes through the expansion valve. The expansion valve restricts the flow of refrigerant. When the high-pressure liquid goes through the expansion valve it enters the evaporator.
- The Evaporator
The evaporator is where the refrigerant starts evaporating back into a gas. When the refrigerant evaporates it gets very cold and absorbs a lot of heat. It is in the evaporator that the process fluid will interact with the cold refrigerant. Heat is removed from the fluid and transferred to the refrigerant. The refrigerant will then enter the compressor and the cycle begins again.
North Slope Chillers

Now that you know how a chiller works, you may be considering your process chiller system options. North Slope Chillers boast the most advanced active refrigeration circuit available. They are easy to install, remove and relocate and will not disrupt the layout of your current system. Whether you’re looking to cool, freeze, or anything in between, North Slope Chillers offers a solution to meet your needs.